Not quite Venice
Not quite Venice, eh?
..
Venetian Glass Blowing
@
M-Space in Tacoma
..
..
So, I reached way beyond my comfort level to try something new. This time it wasn't skydiving but rather glass blowing. I took a class on creating glass floats (the kind of floats traditionally used to suspend fishing nets in the oceans). I stumbled on the class while trying to find more info about a couple of letterboxing classes I've volunteered to help teach at the Tacoma Nature Center the next couple of weeks. While navigating the online class list, I stumbled on several really awesome sounding activities--the one that most caught my eye was the glass blowing class--with a follow on 6-week in depth glass blowing introduction series.
Initially, we dipped the pipe into the 'glory hole' furnace on the right of the photo to 'gather' a layer of molten glass onto the pipe. The glory hole's 'crucible' contains clear molten glass that is specially formulated to allow it to remain malleable long enough to create interesting designs/pieces with it by twisting/blowing/forming.
Traditional 'bottle'/jar glass--such as that used for Coca Cola bottles is designed to cool instantly within molds so it meets exact standards such as a common size at the lid to allow for bottle caps.
The glass we work with today remains malleable for several minutes by continuing to return it to this secondary reheating furnace you see on the left. Every couple of minutes the pipe is returned into the furnace, rotated for a few seconds then returned to the work bench for 'maneuvering'.
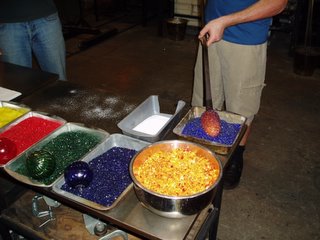
Here, you see the array of 'color' options from which we must choose. The colors range from a bright yellow, deep red, smokey green, purple, mottled yellow/orange/red/white mix, cobalt blue (into which he dips the glass), a neighboring 'frit' layer of white and a hard metal surface upon which he rolls the glass to 'blend' the colors.
Selecting the color was quite a 'commitment'. It was so difficult to decide. What I wanted was a mix of blue, green & purple but I was a bit hesitant to see how the colors would 'blend' thinking it might create browns in places where two colors overlapped. After much deliberation, I decided to go with as much cobalt blue as possible with a slight layer of dappled opaque white 'frit' on the outer layer. You see some of the frit scattered about the top of the table into which he will eventually roll the glass.
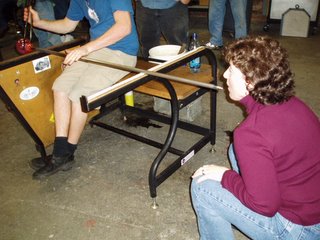
Here, you see the 'work bench'. The color has been dipped, the glass & pipe have been returned to the furnace a couple of times and the process of twisting, turning, and blowing begins. At first, a quick 'puff' of air is inserted into the glass by plugging up the end of the pipe with a finger to cause the glass to swell. The cool air on the inside creates a vacuum and forces the glass to swell like a giant balloon.
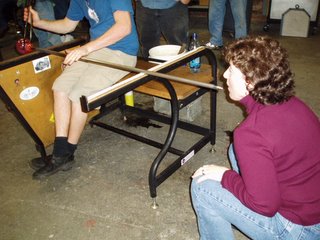
Here, you see the 'work bench'. The color has been dipped, the glass & pipe have been returned to the furnace a couple of times and the process of twisting, turning, and blowing begins. At first, a quick 'puff' of air is inserted into the glass by plugging up the end of the pipe with a finger to cause the glass to swell. The cool air on the inside creates a vacuum and forces the glass to swell like a giant balloon.
The pipe is constantly twirling as the glass is always losing to gravity. The twirling ensures an even, spherical surface.
Here, I blew into the pipe several times to increase the size of the float. It seemed to be about every 25 seconds or so. In between the puffs of air, he continually 'whittled' away the edges with his pliers and other instruments that appeared much like ancient metal working tools you might find in a blacksmith's shop. These tools were used to mold the surface, cool it down and to smooth it as necessary. They also helped force colors into and away from certain areas of the surface.

You see the tools here. Some folks wanted 'swirls' in their floats. The swirls required additional glass on the end of the piece. At a point in the process, they'd use the pliers to pull out a ball shape of the glass and then they'd twirl the glass around to create the pattern--using this extra ball for leverage. Sometimes they'd do double swirls and that would involve the same process twice but in opposing directions and occasionally with different colors of glass. Once the desired swirl was created, then they'd cut off this outer 'ball' of glass, take it back to the furnace to reheat and then smooth out the 'stub' where the piece was removed. One lady insisted on a Washington Huskies Purple & Orange float--it'll be interesting to see what that looks like in the end!

You see the tools here. Some folks wanted 'swirls' in their floats. The swirls required additional glass on the end of the piece. At a point in the process, they'd use the pliers to pull out a ball shape of the glass and then they'd twirl the glass around to create the pattern--using this extra ball for leverage. Sometimes they'd do double swirls and that would involve the same process twice but in opposing directions and occasionally with different colors of glass. Once the desired swirl was created, then they'd cut off this outer 'ball' of glass, take it back to the furnace to reheat and then smooth out the 'stub' where the piece was removed. One lady insisted on a Washington Huskies Purple & Orange float--it'll be interesting to see what that looks like in the end!

Here is my float towards the end of the twirling, blowing process. It probably looks the most like it will finally end up after it cools.
The colors in glass blowing are similar to some glazes in ceramics--in the beginning they don't always look like their final result after they're heated. So, I'm curious to see what the final product will look like.
At this stage in the process, the float is removed from the pipe by placing it onto an asbesto covered work surface. The pipe is 'gently' tapped off. Another worker adds a little 'mound' of additional glass, it's gently heated with a blow torch, a letter stamp is impressed into this mound or a hanging loop is created out of it. From here, it is quickly inserted into the kiln where it is slowly cooled to room temperature. If it doesn't go through this 'tempering' process the glass will cool off too quickly and shatter. Rather interesting process to behold.
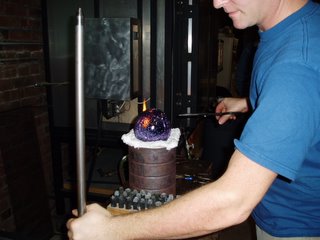
I have yet to see my final glass float. It must temper for at least 12 hours. Hopefully, I'll be able to pick it up in a few days.
It was all a very interesting experience. I learned alot about different color mixing techniques and uses for glass blowing. Quite spectacular to follow the process through from start to finish.
Not a bad way to spend a couple of rainy hours in the Seattle area. ;)
..
By the way, Seattle missed out on breaking its 33-day consecutive rain record yesterday ending up with 27 consecutive days of rain. Odd, though, because it actually rained in Seattle yesterday. The precipitation measurements, however, are taken at Sea-Tac Airport (not exactly Seattle anyway) and their gauge failed to register any rain. So, statistics aren't always as they appear. A good lesson to remember in life! In fact, on Saturday, a day for which we received rain credit, it was practically sunny all day long! We spent much of the day at the beach! Another good lesson in life!
..
The record hunt, however, is still on for the cities of Olympia & Shelton--much closer to where we live than Seattle, anyway. In fact, I can see the city light glow from Shelton at night--that's how close we are to Shelton! Of course, we'd have to be birds or orcas to get there quickly. ;) So, not all is lost! Those two cities probably have a great chance at shattering the record because the forecast continues to call for rain for the next week STRAIGHT! We'll see how far Olympia & Shelton can take it.
...
Again, the irony factor continues! Mt Baker Ski Area was closed for 2 more days because they got TOO MUCH SNOW! Also, the other main regional ski resorts (Stevens Pass, Snoqualmie Summit & Crystal Mountain) all had to turn skiers away from their slopes this weekend because they were TOO crowded! Crazy--because last year each of these ski areas might have had 2 weeks of open ski lifts--at most! When it rains, it really pours!!!
...
Stay safe & never forget the reason for which we celebrate Martin Luther King Jr's life!
That all men are created equal and should be treated as such!!!
1 Comments:
It was great to meet you at the class. I'm going to pick up my float today at lunch.
-Kris
Post a Comment
<< Home